|
|

Fusing
The basic thing that sets Fused Glass apart from other art glass forms is that it is heated in a kiln rather than with a torch (flameworking) or a furnace (blown glass) or never heated (stained glass). Much of the design process is done while the glass is cold, working with sheets of colored glass much like stained glass, or with dichroic glass.
The process begins with cutting colored or dichroic glass into pieces to form a base and all the design pieces and arranging the design in multiple layers. The next step is to fire it to a temperature of 1300-1500 degrees Fahrenheit (depending on the desired result) in a kiln and slowly cool it to properly anneal the glass. Most pieces involve 2-3 firings to get the look and the layers just right. Each firing takes 4-12 hours, depending on the thickness and intricacy of the piece.
|
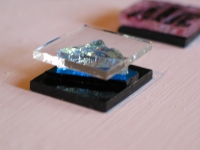 |
Learning the complexities of glass, kiln and firing schedules is a true challenge, and I am continually learning. Finding the right firing schedule for a particular combination of glass can be very elusive and it is like trying to create a formula with a hundred variables. These variables can include (but are not limited to!):
- desired size of finished piece
- number of layers
- sizes of the pieces making up the layers
- the colors of the glass
- the texture of the original glass
- the texture desired in the end product
- and the size of the kiln (I use two - one very small, one 18 inches across by 14 inches high)
This combination of science with art may be what appeals so much to me, as my left-brain still gets a workout figuring out the formula while my right-brain works on the visual end in mind.
After fusing, the work is only half done! Many other techniques are used to finish the glass into a piece of jewelry. This "cold working" can involve grinding, drilling and polishing, and usually the addition of silver or gold-filled wire. Many of my pieces I wrap with silver wire and from the wire, form my own bail.
Dichroic glass
The word dichroic is Greek: "di" means two and "chroic" means color. Originally developed in the 1960's as filters for use with lasers, the main characteristic of Dichroic Glass is that it transmits one color and reflects a completely different color. Furthermore, these two colors shift depending on angle of view and light, making Dichroic Glass not only beautiful, but ever changing.
The unique and brilliant colors of Dichroic Glass are created with special metallic coatings in an expensive, highly technical process. A high-voltage electron beam vaporizes certain types of metals in a vacuum while the glass revolves inside the vacuum and collects layers of molecular films from the metallic vapors. The types of metals used and the order in which they are deposited on the glass are factors that determine the colors that are transmitted and reflected. Some colors have as many as 30 layers of these materials yet the thickness of the total coating is approximately 35 millionths of an inch.
This site and all images copyright © 2008-2017 BarrNone Studio
No portion of this website may be copied or used without the written permission of the artist.
|